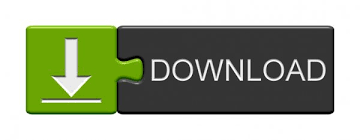

Then, admittedly, went a little overboard on the tiny boxes. As you can see in the opening image of this post! I used the make command to generate STLs for my printer. It works! When I change any of the values I get a new model of the box. Oh no! An error in our code!Īfter fixing the sketch, I tried again. I drew a line from one end of the box to the other, making sure to constrain each of its ends to the middle of the lid, and then used the coincident constraint to attach the middle of the slot to that line. In this case, when I drew the initial slot I didn’t have the midpoint of the slot constrained to the middle of the lid. Like any code, it didn’t compile the first time.
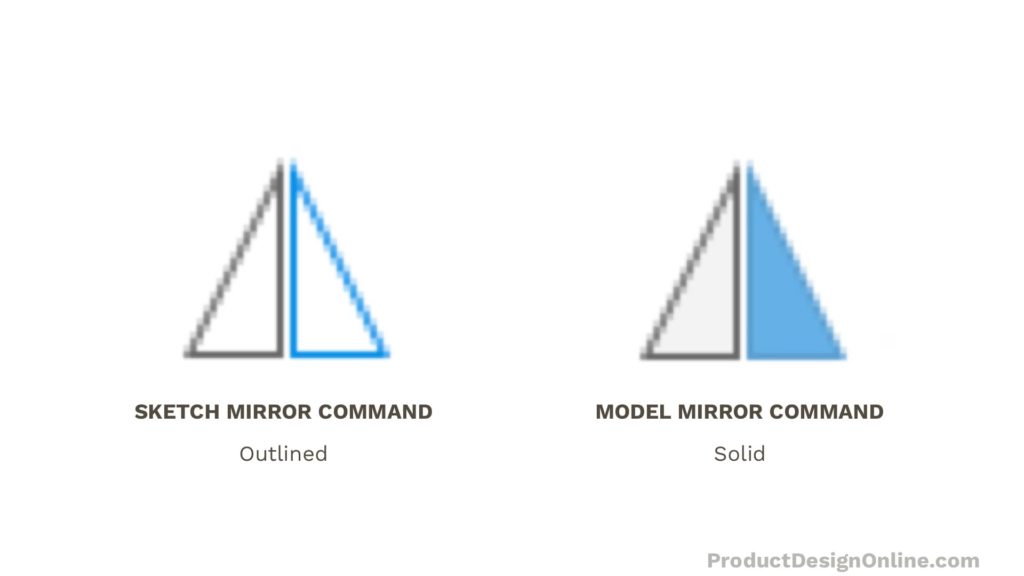
We’ll go back and open the parameters window and change one of the dimensions. After I added the ridges I drew a rectangle that cuts away some of the ridges so I can have an area to write what’s in the box. I used the slot tool to add ridges to the top for grip. This was similar to the previous steps: make a sketch that is dimensioned with the variables, then extrude or cut using the sketch. Next I added some decorative features to the lid. SymmetricalCopy(box_end, plane_of_symmetry) Again, since I want a parametric part at the end, rather than entering numbers during this step I enter in the variables I had set previously. Once the profile of the part was finished I selected the lid profile and the box profile and extruded the box. Note the fx: these are numbers taken from our parameters. However, if the shapes in the sketch aren’t touching they will be extruded as separate bodies.Ī close up of the sketch used to generate this part.
Fusion 360 mirror sketch software#
The constraints tell the software that, mathematically, Line A is always parallel to Line B, or Circle A is always tangent to Line B. One mistake I see a lot of newbies make is to completely ignore the dimension tool (shortcut: D) and the constraints panel. I tend to think of the process as graphical programming. Next came the sketch. When using any modern CAD software it’s important to keep in mind that what you are doing isn’t really drawing as much as it’s building a mathematical model of your object. 0.25mm is pretty easy to hit for a well tuned printer.
Fusion 360 mirror sketch how to#
Another way to describe what we’re going to learn is: How to think when modeling in Fusion 360. I’ll do that in just a minute as I walk you through modeling a simple object. One of the nice features is that it lets me share my models with others. This is web-based 3D Modeling software produced by Autodesk. It’s simpler than it sounds.Įven if you don’t use Fusion 360 it’s good to have an idea of how different design tools work. To do this we will be making a mathematical model of our object and then we’ll change variables to get different geometry. However, it’s possible to get some of that same goodness out of Fusion 360. We all know and love OpenSCAD for its sweet sweet parametrical goodness.
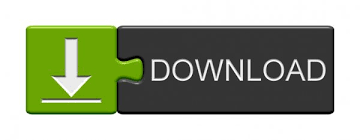